It works for some companies, sometimes.
LSS is a technique for reducing any effort to it's component activities and then analyzing those processes for ways to become more efficient. GE is held up by LSS advocates as a LSS success story. I haven't researched the story, but apparently they experienced a great increase in profits from the use of LSS.
LSS works great if efficiency is your problem. It doesn't work so well if your problem is that you have a lousy marketing department, you signed a bad contract or your business model has grown out of date. LSS requires you to spend a great deal training your people and keep full-time LSS experts on staff. It is presumed that the efficiencies they uncover will pay for the effort. I would argue that this is a fallacy.
An organization using LSS typically prioritizes candidate LSS projects based on their Return on Investment (ROI). It tackles the ones with the best ROI first. Meanwhile, since the LSS experts are on staff, the cost remains constant. The following chart shows what happens over time.
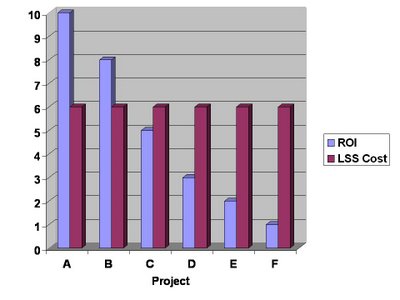
Eventually you get down to the projects whose ROI is less than your recurring LSS costs. After that point, LSS is a loser. How many organizations out there do a good job terminating bad projects? Not many. Most corporate efforts outlive their usefulness by a longshot and internal process improvement ones are no different. LSS is just one more.
Profit is income minus expenses. In gross terms, LSS helps you reduce your expenses by making you more efficient. Expenses have a minimum level. If you manufacture drive shafts, you can't get the steel or machinery for free. LSS will help you asymptotically approach that minimum cost. If you're already close to that minimum cost, then LSS is not a good fit.
I would bet that GE and the other LSS success stories were cases where the companies biggest problems lay in efficiency. If your problem is somewhere else, such as corporate branding, strategic vision or company infighting, then LSS is not the way to go. I would also suggest that LSS eventually wears out its welcome as the chart above shows.
I still don't like it, but at least now I know why. I wonder what our Chancellor of the Exchequer thinks.
For more posts on business, management and such, visit this week's Carnival of the Capitalists.
Actually, unfortunately I think the problem is larger and not as simple as "If your problem is somewhere else, such as corporate branding, strategic vision or company infighting, then LSS is not the way to go." I discussed some of this in Will Six Sigma Fix Bad Management. The huge problem is addressed well by Bob Sutton in Management Advice: Which 90% is Crap?
ReplyDeleteI think Deming's ideas (which are very close to lean thinking) are the best way to go. The critical factor though is the execution of lean, six sigma, process improvement... and often that leaves a great deal to be desired.
It is useful to improve an organization's efficiency. There should be no doubt after reading this post.
ReplyDeleteThanks for the nice blog. It was very useful for me. Keep sharing such ideas in the future as well.
ReplyDeleteHello, i would like to read more information about this topic because i think that is really interesting, besides, the post has very good informaton.
ReplyDeleteWomen lingerie
I was searching some thing relevant to this, And i am feeling lucky, as its the perfect one for what i am looking for. I will share this.
ReplyDeletePropecia 1 Mg.